Total Productive Maintenance
Total Productive Maintenance:
Total productive maintenance is a maintenance management philosophy that strives for total perfection—zero breakdowns, zero defects, zero losses, zero accidents—by positioning maintenance as a core, value-added function rather than a cost center. In other words, TPM reframes maintenance as a business advantage because of its potential to greatly reduce unscheduled downtime and lost revenue.
Total productive maintenance (TPM) is the process of using machines, equipment, employees and supporting processes to maintain and improve the integrity of production and the quality of systems. Put simply, it’s the process of getting employees involved in maintaining their own equipment while emphasizing proactive and preventive maintenance techniques.
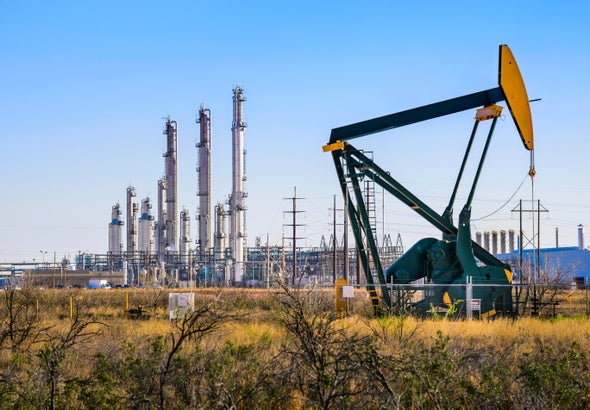
Total Productive Maintenance focuses on the following areas of maintenance:
1.Autonomous Maintenance
2.Planned Maintenance
3.Focused improvement through small group activities
4.Quality Maintenance
5.Early Equipment Management
6.Training
Additional tools used:
- 5S
- Poke Yoke
- OEE
Some unique features of TPM include the following:
- Applies a lifecycle view of equipment employing early equipment management strategies to reduce total cost of ownership
- utilizes maintenance prevention and maintainability strategies to minimize the maintenance requirement
- Incorporates a robust implementation process
- Trains management to be real change leaders
- Creates a defect elimination culture
We have expert practitioners that can assist and guide you through a TPM implementation. Call us for more information.