Consulting and Advisory services
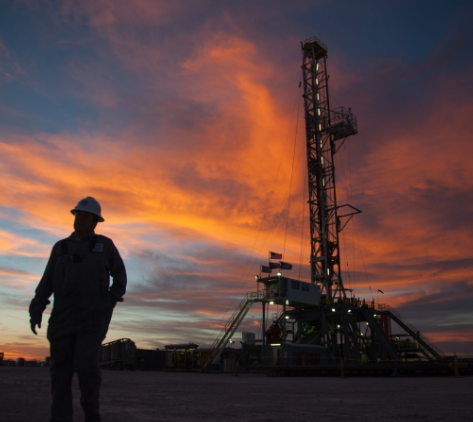
Consulting and Advisory services:
We can target specific needs of a client, after a exploratory discussion using a multitude of interventions. Our typical approach is a 3 step process:
1.Understand: The process begins with a thorough assessment of existing maintenance and reliability practices. Approximately one week is spent observing maintenance activities, interviewing employees, conferring with management, reviewing documentation, touring facilities and becoming familiar with the client’s unique situation and environment.
The resulting examination includes observations, findings and discoveries about all practices assessed which impact your maintenance and reliability program’s effectiveness, including plant condition, equipment availability, work management process, materials management practices, reliability practices and asset management system implementation.
2.Analyze: The next step is to perform a gap analysis. We will review the findings highlighting strengths and weaknesses and compare to best practices in industry. Using our database of World Class metrics, KPIs and industry best practices we can quickly highlight the strengths to build on and the opportunities for improvement.
3.Improve: Once the data is analyzed and it is converted into improvement objectives and initiatives. The improvement initiatives are converted into a implementation plan and roadmap for success. We can either manage the project for the client or support their team in the implementation effort.
Subsequent consulting and advisory interventions will be tailored to meet client requirements. Support for the client will continue until the project is installed and implemented to clients satisfaction.